有很多企業推行了精益生產,但是并不是每一次推行精益生產的企業都取得了精良的結果,這此中就存在著很多對付精益生產的了解誤區:
1、誤區一:精益生產僅僅是一套體系或方法

有 位學員在上完精益生產“9分鐘換模”的實戰案例以后,提出讓照料師幫助把他公司的機器也改成“9分鐘換模”(每年可以節流數百萬),照料費好談。可見,這 位學員以為“9分鐘換模”只是一套可簡樸復制的方法。而究竟是,某企業從三個小時換模時間改進到如今的9分鐘,整整花了近10年的時間,累積了900余項 改進。并且通過這個改進歷程,員工的意識和本領都大大地進步了。只有情況、設置裝備部署、質料、方法和員工等同時具備尺度所要求的條件,如許的結果才可以 大概得到維持。
準確的了解應該是,精益生產是在全員的配合下連續改進的,不是可以簡單復制的。
2、誤區二:豐田可以做零庫存,我們不具備做零庫存的條件
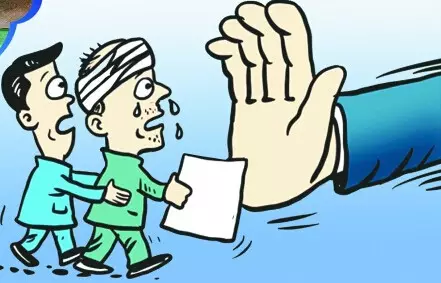
精益生產中常常會提到零庫存,但是卻常常聽到很多學員說,零庫存只存在于理論,以企業現在的狀態不可實現。究竟并非云云,在豐田的堆棧里以及生產線上,庫 存是客觀存在的,只是豐田人一刻也沒有制止對更少庫存(無窮靠近于零)的尋求。可見,零庫存并不是實際,而是一種不停走向精益的頭腦和對零庫存連續尋求的 態度和舉措。
與零庫存相似的另有零缺陷、零浪費、零切換、零停滯、零妨礙、零災害。這七個“零”是目標,而不是實際,所昭示的便是統統尋求完善的精益辦理理念。
3、誤區三:“自動化”便是主動化

曾經不止一次被問到,豐田的生產線主動化比例到底有多高?從題目中可以讀到人們的一個了解誤區,那便是誤把“自働化”當主動化。海內的很多入口翻譯冊本里,也常常殽雜這兩個觀點。
事實是,自働化是豐田生產方法里基本原則之一。所謂自働化,便是讓設置裝備部署或體系擁有人的“智能”。當被加工零件或產物出現不良時,設置裝備部署或 體系能即時果斷并主動制止。通過“自働化”改進的設置裝備部署或體系,可以到達兩個目標,一個是不生產不良品(實現零缺陷),另一個是可以節流監控設置裝 備部署運行的關照人(實現省人化)。所以,“自働化”與一樣通常意義上的主動化不是一回事。
4、誤區四:精益生產便是看板辦理
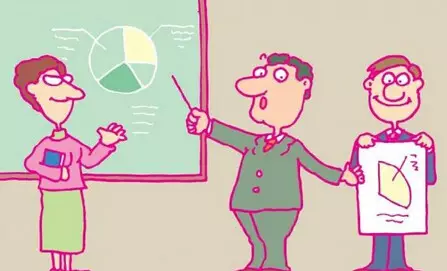
看板辦理是實現后工序拉動式生產,并終極實現定時化的一個東西。
傳統生產,以工序從前望樓的方法推動生產,即前一個工序完成,然后通報到下一個工序。如許做的題目便是當產能不立室時,會出現制品停滯、聚集等題目。精 益生產才有后工序拉動,即后工序用看板關照前工序“什么時間?必要什么?必要多少?”;前工序憑據后工序的需求和節奏擺設生產,保障供應。
除 此之外,另有許很多多的了解或辦理誤區攔阻我們走向精益。好比,有人以為員工責任心太差,做不了零缺陷;供應商辦理程度太低,做不了零庫存;所處行業特 別,做不了精益生產等等紛歧而足。此中以“條件論者”為多數,在我看來這些論調都屬于拒絕走向精益的托詞。殊不知,豐田是在決定生產汽車的1926年提出 了“自働化”和“JIT”的管理原則,并持續改善至今。